When you’ve been in the industrial coatings industry and protecting the nation’s penstocks, power plants, and bridges as long as Thomas Industrial Coatings has, you find yourself making a lot of big choices that can have huge impacts on the way you do business. One choice we made long ago was the decision to own all of the equipment we use rather than lease bits and pieces of it. That one choice alone has given us an incredible competitive edge over other industrial painting and coating companies.
So how can a simple thing like owning and investing in our own equipment give us such an advantage?
1. Mobility
You receive two things when you’ve been hired for a coatings job: a contract and a deadline. To the client, that deadline is everything. Nothing else can progress as scheduled until your tasks have been completed. The last thing they want to hear is that you’ll have to push back the timeline on the penstock preparation you promised because the local equipment rental company is backordered on a V-60 6-pot reclaiming unit.
Owning and properly maintaining our own equipment means we can get out to the job with minimal delay. That allows us to get to work more quickly than some other industrial paint and coatings companies, which means we have a better chance of coming in way under that pesky deadline and putting a smile on our customer’s face.
2. Preparation
Proper planning is essential in this industry. After all, by building and following a solid plan of action on the industrial coating job site, you’re helping to ensure the quality and efficiency of the work, as well as, most importantly, the safety of everyone involved in its completion. So why not take the time to plan for the future of your business?
By owning and constantly investing in the equipment we use through upgrading, maintenance and even replacement, we can ensure that each and every part of our fleet is ready for anything, whether it’s the job we’re doing today or the one we’re working on two or three years down the road. It might seem expensive, but the benefits of this kind of preparation can’t be denied. Equipping our workforce with the latest gear makes our employees more agile and efficient, which allows them to take the quality of the work to the next level.
You can’t plan for everything, obviously. Sometimes you need to lease out something to complete a job where even the best-maintained piece of equipment has failed you. But while leasing can be a boon in the short-term, it becomes increasingly difficult to face future challenges when you’re depending on another company to supply you with the tools you need to tackle them.
3. Familiarity
Like a good partner, you get to know the equipment you use over time. You train on it. You get to know how it works and how best to get the job done together. You can tell when it’s working at peak performance or when something’s wrong just by flipping a switch. That kind of familiarity only comes when you own the equipment you send out with your crews.
When you’re constantly leasing pieces of equipment, it can be like forcing your crews to dance with total strangers. They may be similar to what they’ve worked with before, but they don’t know its quirks, how well it’s been maintained, or whether it’ll perform at the levels they’re used to. That can lead to mishaps and mistakes on the site, all of them time-consuming and some of them even dangerous.
The workers here at Thomas Industrial Coatings are constantly training and re-training with their equipment, learning new tactics and reinforcing the best practices every day. A complete working knowledge of the tools of the trade makes them safer, more effective, and highly proficient in every way.
When you’re good at what you do, you’ve gotta own it
We understand that there are great reasons to rent or lease equipment sometimes. But we here at Thomas Industrial Coatings believe that for a company like ours to be truly successful, one has to make the commitment of ownership and investment when it comes to tools and equipment. By choosing to do so, we’ve gained a more experienced crew that arrives at the job site quicker and better prepared to meet our client’s needs, and we can do the same for you.
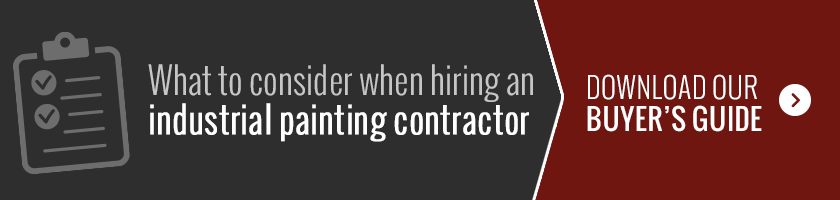